Coreless Melting Furnaces
Coreless Induction Melting Furnaces
Induction furnaces provide an economical method to melt and hold large quantities of molten metal. A high-frequency induction coreless furnace is a furnace with no core, containing a refractory lined, insulated multi-turn copper coil (carries the AC current that generates the electromagnetic field), a steel shell (main support), insulated top plate, yokes/shunts (stacked thin strips of highly magnetic silicon steel acting as an electromagnetic flux return path to contain the electromagnetic field), the bottom faraday ring or flux plate (shields the magnetic steel floor), and the top faraday ring (shields the magnetic steel lid, top plate, and shell from the electromagnetic field). Below are some popular coreless designs, as well as power supplies, to accommodate different ferrous and non-ferrous applications:
- Steel Shell Furnaces
- Steel Frame Furnaces
- Box Furnaces
- Lift Swing Furnaces
- Lift Coil Furnaces
- Hand/Tabletop Furnaces
- Rollover Furnaces
- Lab Furnaces
- High Power Density (HPD) Furnaces
- Super Heaters
.png?width=1280&height=721&name=Melting-Coreless-Rolled-Steel-Shell-4_1080x607px%20(1).png)
.png?width=1280&height=721&name=Melting-Coreless-Pillar_1080x607px%20(1).png)
.png?width=1280&height=721&name=Melting-Coreless-Stainless-Foundry_1080x607px%20(1).png)
.png?width=1280&height=721&name=Melting-Coreless-30-1080x607px%20(1).png)
.png?width=1280&height=721&name=Melting-Coreless-Donsco-10ton-7MW_1080x607px%20(1).png)
%20(1).png?width=1280&height=721&name=Melting-Coreless-Navy-100ton-tilting_1080x607px%20(1)%20(1).png)
.png?width=1280&height=721&name=Melting-Coreless-Chilca-Peru-Powershare_1080x607px%20(1).png)
.png?width=1280&height=721&name=Melting-Coreless-Navy-100ton-tilting-open-hood_1080x607px%20(1).png)
.png?width=1280&height=721&name=Melting-Coreless-Steel-Shell-Lectrotherm_1080x607px%20(1).png)
.png?width=1280&height=721&name=Melting-Coreless-Open-Steel-Frame_1080x607px%20(1).png)
.png?width=1280&height=721&name=Melting-Coreless-Box-Furnace_1080x607px%20(1).png)
.png?width=1280&height=721&name=Melting-Coreless-Lift-Swing_1080x607px%20(1).png)
.png?width=1280&height=721&name=Melting-Coreless-Lift-Drop-Coil_1080x607px%20(1).png)
.png?width=1280&height=721&name=Melting-Coreless-Hand-Tabletop_1080x607px%20(1).png)
.png?width=1280&height=721&name=Melting-Coreless-Rollover_1080x607px%20(1).png)
.png?width=1280&height=721&name=Melting-Coreless-HPD_1080x607px%20(1).png)
.png)
.png)
.png)
.png)
.png)
%20(1).png)
.png)
.png)
.png)
.png)
.png)
.png)
.png)
.png)
.png)
.png)
Providing Heating & Melting Solutions Since 1916
Steel Shell Furnaces
In a rolled steel shell furnace, the body is constructed from heavy steel plate rolled into a cylinder, providing maximum strength for the entire furnace shell assembly. Flux return yokes are bolted directly through the furnace shell to support the power coil. The superior strength of the shell provides support for the furnace components, especially while tilting for pouring. The forces are tied directly to the shell of the furnace, not through the coil and refractory, maximizing refractory lift. The bottom of the furnace is secure with a heavy gauge aluminum bottom plate, and a water-cooled copper ring is placed above the cooling coil to prevent stray heating and minimize electrical losses.
.png?width=570&height=356&name=Melting-Coreless-Steel-Shell-Lectrotherm_570x356px%20(1).png)
Steel Frame Furnaces
Open steel frame furnaces are designed for maximum-duty iron melting applications. The stresses on the coil and refractory can be severe under these high-power density applications. To meet these demands, we designed a rugged, open steel frame for durability and ease of access. Hollow bar copper tubing is used for coil integrity and tie rod construction is utilized to compress the coil within the steel frame, ensuring minimal movement of the coil and refractory.
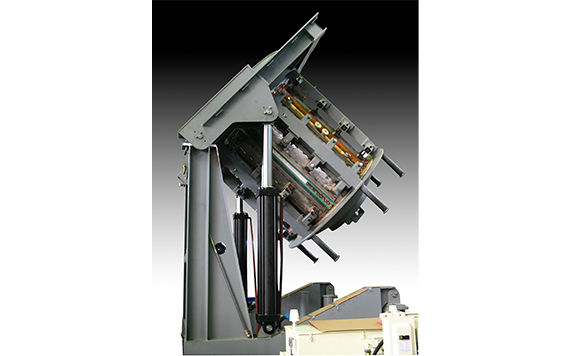
Box Furnaces
The flexible box furnace design includes removable side panels and through bolt connections for easy coil access. The hydraulic tilting assembly uses high-quality cylinders, industrial tilt control valves, and flow valves that ensure a controlled descent rate. The tilt angle is a full 105 degrees for easy removal of all molten material. The box furnace is available in either standard or nose tilt designs.
.png?width=570&height=356&name=Melting-Coreless-Box-Furnace_570x356px%20(1).png)
Lift Swing Furnaces
The lift swing furnace, or swinger furnace, provides fast, clean, and efficient melting for non-ferrous alloys. In this two-crucible design, the operator moves the coil, not the crucible full of molten metal, permitting a convenient, rapid alloy changeover without fear of material contamination.
.png?width=570&height=356&name=Melting-Coreless-Lift-Swing_570x356px%20(1).png)
Lift/Drop Coil Furnaces
The drop coil furnace is designed for use with a single, free-standing crucible for melting non-ferrous metals. Features include a high-efficiency coil, fabricated steel furnace base, confinement area, refractory pedestal for crucible support, pneumatic cylinder, and flow control valves.
.png?width=570&height=356&name=Melting-Coreless-Lift-Drop-Coil_570x356px%20(1).png)
Hand/Tabletop Furnaces
The hand/tabletop furnace is ideal for small melting requirements, precious metals, laboratory processes, and assay determination. The design incorporates a refractory fiber-reinforced shell, top, and bottom. The induction coil is terminated for use with water-cooled leads. The hand furnace is also available with a hydraulic assist for tilting larger quantities of material.
.png?width=570&height=356&name=Melting-Coreless-Hand-Tabletop_570x356px%20(1).png)
Rollover Furnaces
Rollover furnaces offer the investment caster control over speed of rotation, repeatability, accuracy, and is even able to set the mold clamping force through the use of an electric servo driven motor or hydraulic actuator.
.png?width=570&height=356&name=Melting-Coreless-Rollover_570x356px%20(1).png)
High Power Density (HPD) Furnaces
A high power density furnace is a coreless furnace designed to operate at power levels above the normally accepted levels for a given furnace size. These furnaces come in a structural, open-frame stud-less coil design for maximum durability and rigidity. The wide body provides better access to slag or dross buildup on furnace walls and the ability to load larger, bulkier, lower-cost scrap.
.png?width=570&height=356&name=Melting-Coreless-HPD_570x356px%20(1).png)
Resources
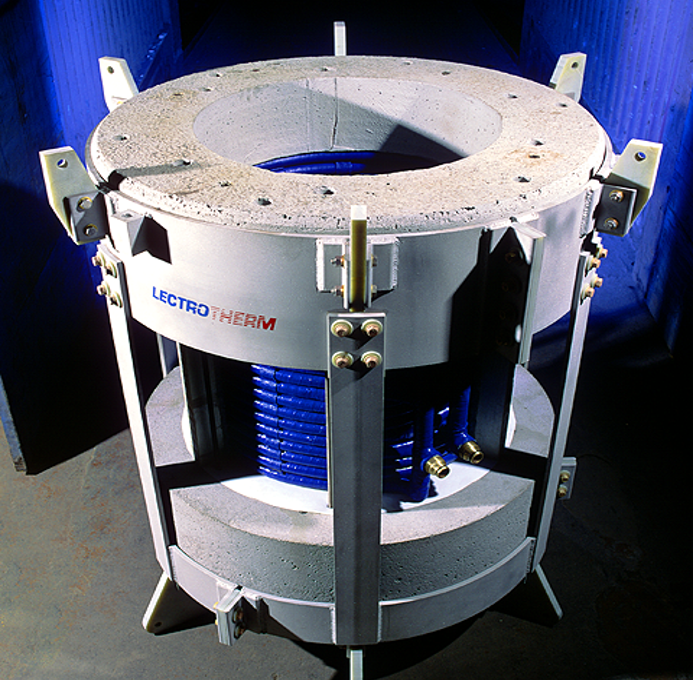
Induction Related Considerations in Investment Casting
Aug 24, 2007 by Ajax TOCCO MagnethermicLearn the basics of induction and how induction furnace systems play a critical role in investment casting.
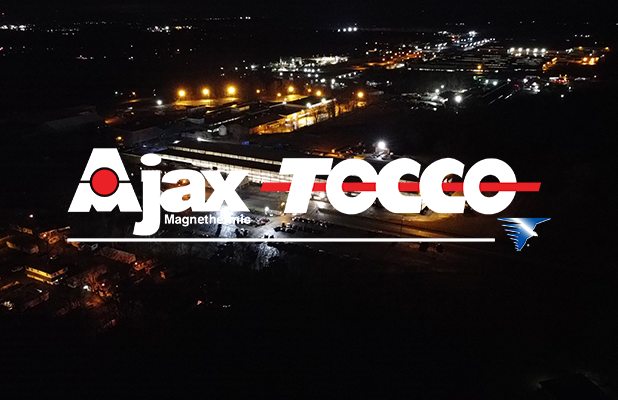
European Recycler of Precious Metals Orders Two Medium Frequency Coreless Induction Melting Furnaces from Ajax TOCCO Magnethermic
Aug 22, 2013 by Ajax TOCCO MagnethermicLearn how Ajax TOCCO helped a recycler of precious metals replace their existing furnaces with two medium frequency coreless induction melting furnaces.
Thank you for requesting access to this brochure.
You can access your download by clicking here.