2 min read
Successful Start-up of Two 350T Hot-Dip Galvanizing Pots for Automotive Line at European Steel Strip Producer
Ajax TOCCO Magnethermic
:
October 16, 2013
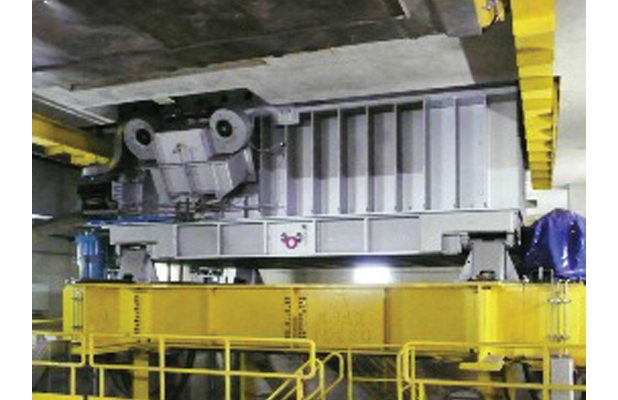
Ajax TOCCO Magnethermic successfully started up the Phase Two galvanizing equipment for an automotive line at a major steel producer in Europe. The line is now able to produce galvanized strips with two types of coating alloy.
In 2009 Ajax TOCCO Magnethermic supplied and commissioned the Phase One part of the project working in conjunction with a major steel industry line builder, which consisted of the following.
Coating pot with a zinc capacity of 350T which was rated at 1000kW and equipped with two 500kW “TE” Jet-Flow inductors. The coating pot was statically mounted on the lift platform initially, but designed to allow for easy integration of transfer bogie wheels for mobilization in Phase Two
- Hydraulic lift platform for raising and lowering the coating pot between the operating and the down (off-line) positions, allowing for easy and safe access to the snout for maintenance work.
- Platform/pot movement control panel was designed and supplied for dual pot capabilities, allowing quick conversion from Phase One to Phase Two
- Snout access platform that also operated as an insulating cover for the coating pot when in the down (off-line) position. The snout access platform was mounted to the ceiling of the cellar on rails and motorized to allow movement over the coating pot when it is in the down (off-line) position. This meant maintenance on the snout could be performed safely above the coating pot.
- 7 T/h ingot charger, with close loop with metal level detector to keep constant metal level in the pot +-2mm. The charger was designed with an 8 ingot storage conveyor system.
In 2012 the customer awarded Ajax TOCCO Magnethermic directly with an order for the Phase Two conversion, which included adding a second coating pot for zinc aluminum magnesium alloy. The Phase Two equipment, supplied and commissioned in 2013, consisted of the following.
- Transfer bogie wheel set to mobilize the Phase One coating pot. These allow for horizontal movement from the down (off-line) position to an ambush (park) position, thus allowing the other coating pot access to the lift platform and the operating position.
- Flexible power cables to replace the existing fixed cable, which allowed the horizontal movement of the coating pot between operating and ambush (park) positions.
- Mobile coating pot with a zinc capacity of 350T that was rated at 1000kW and equipped with two 500kW “TE” Jet-Flow inductors. The coating pot was designed for operating with zinc aluminum magnesium alloy. It was supplied complete with transfer bogie wheels, flexible cables, and services to allow the coating pot to move between operating and ambush (park) positions.
- Coating pot ambush cover. This is an insulated cover that is mounted to the ceiling of the cellar above the ambush (park) position to reduce the heat losses for the coating pot. It also protects the cellar ceiling from radiated heat.
Phase One (single, static position coating pot)
Phase Two (dual, mobile coating pots with horizontal transfer bogie system)
Ajax TOCCO Magnethermic, a subsidiary of Park-Ohio Holdings Corp., designs and manufactures world-class induction heating and melting equipment for various industries and applications throughout the world. In addition, the company provides a range of services and offerings including laboratory process development, preventive maintenance, equipment repair and parts, coil repair facilities, and installation services through its locations in North America, South America, Europe, and Asia.
E-mail: info@ajaxtocco.com
Website: www.ajaxtocco.com