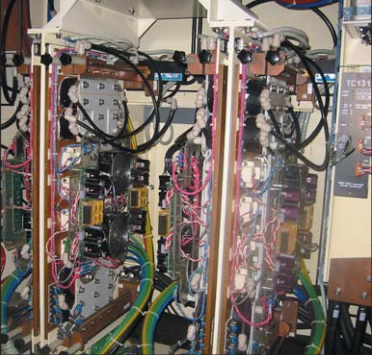
Author: George Pfaffmann, FASM, Equipment & Hardware Materials Technology Subcommittee, ASM Heat Treating Subcommittee, Ajax TOCCO.
Publication: Heat Treating Progress; Nov/Dec 2006
The charter of the ASM Heat Treating Society’s R&D Committee is to identify future technological needs of the heat treating industry and develop the mechanisms to plan, fund, and implement R&D programs to meet these needs and transfer the results of these programs to the industry.
This is the third article in the series highlighting the work to update the 2004 Heat Treating
Technology Roadmap developed to achieve the Vision 2020 goals. The subcommittees
of the Research & Development (R&D) Committee of the ASM Heat Treating Society (HTS)
have revised the four categories of the Roadmap: Equipment & Hardware Materials Technology, Process & Materials Technology, Energy & Environmental Technology, and Institutional Initiatives. This article discusses the modifications to the R&D needs for the Equipment & Hardware Materials Technology section, and highlights some examples of industry activities contributing to meeting Roadmap goals.
The Equipment and Hardware Materials Technology Subcommittee reviewed the updated Vision 2020 initiatives, including a wide variety of specific objectives in the areas of process control, materials, and equipment (hardware) to gauge progress made in these areas. This review is intended to show trends that drive progress or improvements, and more importantly, to determine how progress can be accelerated to leapfrog innovative concepts. Some of the drivers include:
- Improvements in equipment and hardware are largely driven by improved process technology and process-control/monitoring capability. Materials used in heat treating contribute significantly to progress in this area based on reduced costs, efficiency of operation, and equipment capability improvements.
- Hardware/equipment durability and performance are dependent on the proper implementation of process improvements and control enhancements.
There is increasing demand in today’s industrial manufacturing environment for shorter launch times, leaner operating budgets and personnel availability, and increased system sophistication. Added to this is the demand for implementation-ready technology.
State Of The Situation
Many gains in equipment and hardware are related to perfecting/improving existing, well-established processes. For instance, we are seeing a conversion from atmosphere carburizing to vacuum carburizing and high-pressure gas quenching. Processing improvements are being made in the powder-metallurgy industry in using higher temperature sintering, high-velocity compaction, orbital forging, and warm-powder compaction. In addition, new heat treating furnace technology offers improved precise temperature control for heat treating large aluminum components using new types of combustion heating systems. These are examples of gains that have been made by expanding the capabilities of existing technology, and they are important contributions. However, meeting Vision 2020 objectives must be accelerated to make the U.S. heat treating industry more globally competitive and to make it a stronger contributor to maintaining an industrial leadership position in the world. Heat treating by and large has been and still is an experienced-based technology, and this paradigm must be changed to a substantially more structured scientific-based model, which requires that companies capitalize on the tools that are rapidly coming downstream.
Such a concept is cited by the National Science Foundation Blue Ribbon Panel that evaluated simulation-based engineering science (SBES) and its potential to drive progress in a structured scientific approach. The report notes that SBES-related technology will affect every field of engineering and science, but it may have its greatest impact in the field of materials (materials processing could also be added). Modeling and simulation are transforming the capability to improve existing and to develop new materials (and processes).
Heated tube prior to hot gas forming.
Plastic strain profile of formed tube (with close-up of formed area).
Examples
SBES effectively and more efficiently drives, motivates, and optimizes developmental progress. Two examples of technology developments that illustrate the strength and innovative capability of a structured scientific approach are hot metal gas forming and single precise frequency induction hardening.
Hot metal gas forming (HMGF) using induction heating offers improved capability and flexibility over that of the hydroforming currently used to make automotive structural members. HGMF uses intelligent forming, programmed to capitalize on both high heating rates and high strain rates that complement improved plasticity.
Hot metal gas forming is a process that uses in situ induction heating and combines the concepts of hot blow forming used in the plastics industry to form plastic containers and superplastic forming used to manufacture aerospace parts. The process offers a lower-cost manufacturing approach and improved formability to handle complex shapes for a full range of ferrous metals (including high-strength steels) and nonferrous metals. It also has the additional capability of selective profile-based transformation strengthening of ferrous components.
Over a period of about three years, a multidiscipline joint-venture team performed comprehensive material formability studies at elevated temperatures of both ferrous and nonferrous materials. This included uniaxial and biaxial tensile tests together with lab scaled-up prototype tube-formability studies using induction heating at high temperatures and high strain rates to validate computer simulation models for both formability and induction thermal profile analysis. A full-scale prototype in-line production facility was built to replicate realistic production operating parameters. The concept is now in the commercial implementation-ready validation phase.
Of particular significance in the program were the lessons learned regarding the importance of using simulation-based engineering science. Also, it must be driven by validated material characterization at the thermal logistics and at the applied high strain rates used. It was learned early in lab validation tests that the existing knowledge base led to wrong conclusions; that is, the concept could not be optimized or be effectively applied to the complex shapes used in industry today using an empirical or chance approach. It required an assessment of the latest computer simulation tools, and had to be driven by a pedigreed materials-property database. The data had to be generated first before proceeding. Required material data at high temperature/time excursions and accelerated strain rates for specific applications were generated using a specially implemented high-speed Gleeble (Dynamic Systems Inc., Poestenkill, N.Y.; www.gleeble.com) system. This demonstrated hot metal gas forming could be successfully applied to meet part design requirements within the material and process capability parameters.
Single precise frequency induction hardening of gears uses actual distributed high-power saturation density to dynamically program thermal energy properly along the tooth face width. The system generates the required depth of root strengthening without tip overheating. It capitalizes on the use of short heating time with consistent dimensional control plus substantially increased dimensional rigidity (size change) to capture maximum retention of residual compressive stresses for enhanced gear performance. Understanding clearly how to apply the technology required a complete knowledge of the thermal dynamics and energy distribution logistics to optimize the process. This was supported and effectively accomplished by in-depth, comprehensive computer simulation studies.
The technology uses a specific frequency adjusted to match the tooth geometry (diametric pitch/module) to proportion the proper ratio of tooth vs. root heating. This capability can also compensate for thickness on ring-type part configurations (i.e. the geometric mass behind the root that can substantially affect energy input to the root).
Implementation of this technology is made possible by new developments in the power source. Technology advancements led to flexible, programmed high output power (HOP) solid-state variable tunable power supplies using improved capability IGBT devices having a unique innovative programmable device firing arrangement. The equipment is coupled with advanced inductor tooling to produce the required results and still achieve safe operating parameters for required tooling durability and performance. This included simulated computer design optimization for proper heat flux intensity within allowable limits.
The significant accomplishment of this combined technology development is that it was not intuitively obvious. The combination of process and equipment capability requirements evolved from computer parametric studies and various engineered simulation analysis to establish and develop the proper optimum combinations of process parameters and equipment capabilities. Benefits of the development include:
- Capability to handle a broad range of gear geometries
- Substantial reduction and equipment capital investment
- Reduced complexity in equipment design and adherent simplification of process control, which translates to more reliable, consistent quality assurance
- Reduction in equipment complexity, which translates to more user-friendly operation with onboard diagnostics for more effective and efficient reliability and maintainability
As a result, this technology expands the opportunity to transfer a greater number of the surface treatment applications, particularly on gears, from existing fossil- and gas-fired energy supplies used both in atmosphere and even vacuum-carburized technology operations to induction hardening. The encouraging innovation in some recent developments indicate that the process is successful in producing gears having equivalent or higher performance capabilities using plain carbon steels with no sophisticated prior treatments.
These examples provide a perspective of what has been accomplished and what is capable of being accomplished in the future, as well as how we could improve our progress. More importantly, it will hopefully provide the impetus for improved communication and collaboration within the R&D environment to accelerate our progress.
Equipment & Hardware Materials Technology Section Initiatives
Process Control
- Develop improved predictive tools, such as computer models for process
design conditions, thermophysical, and mechanical properties. - Develop real-time process controls, such as smart sensors inside the furnace and quench bath to measure gas flow, quench severity, and carburizing and nitriding potential.
- Develop a direct way of measuring surface carbon in a part in real time.
- Develop nonintrusive remote monitoring of process parameters.
- Develop faster, nondestructive, lower-cost case depth measurement
techniques for all processes. - Develop better systems to survey furnaces to AMS specs (using different sensors and techniques). Note: AMS = SAE Aerospace Material Specification.
- Develop better diagnostic equipment for preventive maintenance, such
as better burner crack detection to prevent furnace atmosphere deterioration. - Need standardization/research on ability to predict equipment variability, as no two furnaces are alike.
- Develop predictive model for furnace equipment including effects of
geometry, fan speed, load sizes, and load configuration.
Materials
- Improve oxygen probe resistance to carbon deposits. Need R&D on
probe materials to operate below 760°C (1400°F). - New functional materials (e.g., insulation) and structural materials (e.g.,
materials for higher processing temperatures). - Optimize cost effectiveness of alternative heat-resistant materials for
furnace components. - Optimize performance of alloys used for heat treating furnace components, such as use of a cost-effective coating for alloy fixturing to improve resistance to carburization.
Hardware (Equipment)
- Develop much higher indirect burner efficiency (80+%).
- Develop a heating system that provides higher heat transfer to the workload; including larger heat transfer surface area, high-flux-rate heat exchanger, and a high-rpm, high-temperature fan for increased convection rates.
- Develop less expensive insulation material to reduce furnace heat loss,
thus improving overall efficiency. - Develop an atmosphere gas carburizing system that requires less heating
energy to eliminate potential to produce intergranular oxidation (IGO). - Develop improved quenching systems for aluminum parts.
- Develop a way to design a quenching system so it can be customized to uniformly quench a complete load.
- Develop improved quench equipment designs based on modeling.
- Develop next generation of heat treat equipment for one-piece flow to support synchronous (lean) manufacturing.
- Develop crack detection sensing capability within the induction heating machine that can sense cracking during induction hardening at a cost less than post-processing inspection.
- Develop low-cost nondestructive method of measuring residual stress.
- Develop improved degreasing equipment, including fluids and nonliquid thermophysical methods of cleaning parts that are more effective yet still cost-effective.
Temperature profile of gear tooth using single precise frequency induction hardening.
Advanced design IGBT trays.
Power source panel frequency display.